The Ezz Steel plant in Alexandria – Al Ezz Dekheila Steel Co. (EZDK) – is a fully integrated steelmaking facility. It incorporates three direct reduction plants for producing high-quality Direct Reduced Iron (DRI), with an annual production capacity of 3.1 million tons, as well as electric arc furnaces coupled with continuous casting for billet and slab production. Rolling and strip mills produce rebar, wire rod and hot rolled coils (HRC). The combined output of the long and flat steel plants is 3.2 million tons per year.
The Alexandria plant is located on the Mediterranean coast of Egypt, with excellent deep water and road connections, enabling raw materials to arrive and finished products to be dispatched efficiently every day by ship and truck.
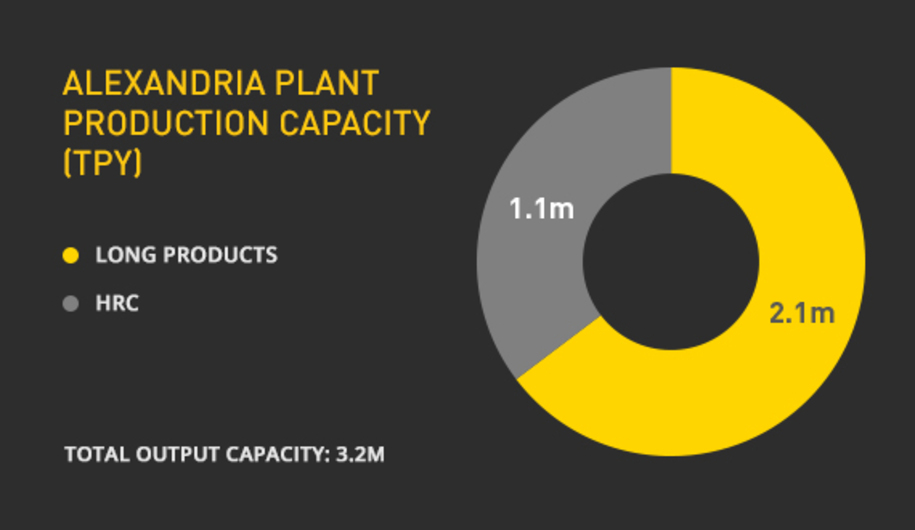.jpg, /rails/active_storage/representations/eyJfcmFpbHMiOnsibWVzc2FnZSI6IkJBaHBBbjBCIiwiZXhwIjpudWxsLCJwdXIiOiJibG9iX2lkIn19--f03d273484a9602d8e7ba4924cfd93e672611b85/eyJfcmFpbHMiOnsibWVzc2FnZSI6IkJBaDdCam9MY21WemFYcGxTU0lKTVRjM01BWTZCa1ZVIiwiZXhwIjpudWxsLCJwdXIiOiJ2YXJpYXRpb24ifX0=--b0fb71633f12b9de8fe3506c0364ae468d59da05/Alexandria%20PLANT%20PRODUCTION%20capacity%20(TPY).jpg 2x)
Integration at EZDK
EZDK operates a dedicated mineral jetty in Dekheila port, which can receive and unload vessels with capacities of up to 160,000 tons of iron oxide pellets. These raw materials are transported direct to the plant by conveyor belts. The unloading capacity of the port facilities is 6m tpy, and the storing capacity of the stacking yards is 660,000 tons. The equipment used in unloading and handling the raw materials include 2 gantry cranes with unloading capacity of 1400 t/h each, two stackers, two reclaimers, a combined stacker/reclaimer, and a network of conveyer belts for material handling.
The iron ore (oxide pellets or lump ore) is reduced in three direct reduction plants (DRPs) using Midrex technology. This energy-efficient process uses natural gas reforming to produce the reducing gases (CO and H2).
Long products production at EZDK
Steelmaking
Molten steel is produced by four, 80-ton Electric Arc Furnaces (EAFs) each with a 58/70 MVA transformer, with the ferrous charge comprising approximately 80% DRI and 20% high-grade steel scrap. The molten steel is refined in three ladle furnaces, which ensure tight control of chemical composition, low levels of inclusions and homogenous chemistry and temperature.
Three, four-strand continuous casting machines transform the molten steel into 130mm2 billets with lengths of 8 and 16 meters.
Long products mills
Our Alexandria plant has two bar mills which produce plain and deformed rebar for concrete reinforcement, available in diameters ranging from 10mm to 40mm in lengths from 6 meters to 24 meters and bundle weights from 2 to 4 tons.
Bar Mill 1 comprises a 130-ton per hour billet reheating furnace, 16 continuous rolling stands and finishing facilities. Bar Mill 2 has a 70-ton per hour reheating furnace, 18 continuous rolling stands and finishing facilities. Both mills use a Quenching and Tempering Box (QTB) which ensures excellent mechanical properties.
The high-speed wire rod mill at Alexandria plant – with a maximum design speed of 100m/sec. – produces plain and deformed wire rod for concrete reinforcement and cold drawing. The mill has a 150-ton per hour reheating furnace, 11 continuous rolling stands and a two-strand rolling line of 14 stands each, water-cooling zones and air-cooled Stelmore conveyors.
HRC production at EZDK
Steelmaking
Molten steel is produced by a 160-ton Electric Arc Furnace (EAF), with 152/182 MVA transformer, with the ferrous charge comprising approximately 80% DRI and 20% high-grade steel scrap. The molten steel is refined in a ladle furnace (LF), which ensures tight control of chemical composition, low levels of inclusions and homogenous chemistry and temperature.
Compact Strip Production (CSP)
An up-to-date SMS Demag Thin Slab Caster (TSC) transforms molten steel into slabs with widths from 900mm to 1600mm. The caster is equipped with Liquide Core Reduction (LCR) technology to produce slabs with thicknesses ranging from 48mm to 70mm. The facility includes a Mold Monitoring System (MMS) and Dynamic Solidification Control System (DSC).
Hot Strip Mill (HSM)
Our Alexandria plant surpasses international standards in HRC production with its innovative hot strip mill, which consists of six stands producing 1.1 million tons of HRC per year. The plant produces precise product attributes, with thickness ranging from 1.0mm to 14.0mm and coil weights ranging from 5.5 to 28 tons.
The facility includes Measuring House, Parsytec and a run-out roller table equipped with super reinforced water-controlled laminar cooling / edge masking, which guarantees a rigorous thermomechanical process for improved mechanical properties in the finished coils.
Skin Pass Plant (SKP)
This plant creates a high-quality product by improving the flatness of thin gauge HRC to meet client expectations.
Processing Center (PC)
The plant’s processing center incorporates a Steel Service Center (SSC) that prepares materials to exact client requirements, whether coil, slit rings or cut-to-length sheets. In addition, a push-pull Pickling Line (PKL) with Acide Regeneration Plant (ARP) offers a product with exceptional surface quality, with no oxide layer, either oil-free or oiled.